This is a guest post from Jay Wise, going behind the scenes of the most audacious Alumni Corps performance that DCI has ever seen. This post has been lightly edited for clarity and style.
At some point in the winter, the design team decided that we’d go find and use two of the slide ramps from 2016. The intent was to replicate the Flugelhorn solo in the same manner with the props back to back. And craftily, the props would hide the drumline during the brass-only Creep and Boxer introduction. They’d move again and be used later in the show too. When you talk about props and set design, Bluecoats are the recent innovators. It was important to reflect this in our alumni anniversary show.
Mike Scott was able to locate the ramps and began the game of getting them “back home” for us to use in the Alumni Corps show. The tale of getting them here and on the field is indicative of the ups and downs of this project and how it almost didn’t happen. And maybe in a larger sense, symbolic of the corps history of getting knocked down and getting back up.
As the 50th Anniversary has had so many moving parts, not just with an alumni corps but with other projects happening, the deal didn’t get closed on purchasing the slides back until mid-June. There were still seven weeks until we needed them in August. Overlooked by me, and perhaps others, in the original e-mail on this deal, was that the slides had been modified. There was also a simple miscommunication on them that would lead to additional issues on our end.
Throughout June we were trying to figure out how to get them back to Canton. One thought was us going to get them in Denton, Texas. The junior corps didn’t have the resources to do it (tour was about to start). Alumni didn’t have the right people with the necessary abilities that had time off. We thought about alumni corps member and truck driver Mike Ruth coming up with them for rehearsal from his home in Texas or sending our other alumni corps member and driver Kevin Stone. But to get these props here would require four to five days of transit. That wasn’t in the cards. The ramps would only fit in a semi-trailer, so someone like me taking a week to go get them in a box truck wasn’t a possibility either.
On June 21st we reached out to FLASH Visual Media in Oklahoma to digitally print the backdrops and vinyl for the slides (which they had done before). So we had the props and now we had the media ordered to finish the set design out. Would they arrive on time?
It took until July 8th to set the plan for the slides moving from Texas, and be added to some of our backdrop frame pickup (also from a band in Texas). This route would run through North Carolina where the rest of the backdrop frames would be constructed. The truck making this cross-country run arrived at the Bingo Hall in North Canton on Sunday, July 31st, and was met by a crew of local alums to unload.
The unload of the ramps was tricky, as there was only a quarter inch of space side to side to move the ramps and an inch or so at best top to bottom. But we got them off and on the ground. And then we realized a significant problem.
The wheels were in the wrong place.
They were not underneath the prop, they were on the BACK of the prop. So you moved the prop and then flipped it up to make it downside up. That was a problem. We called David Glasgow and he walked the two blocks from his house and we started to analyze the problem. When we asked for the “movable” slides, the band selling them to us thought, yeah, they’ve got wheels, they are movable. Turns out we ended up purchasing two of the slides that never moved during the show. Once they were dropped in place, they stayed that way the entire show. So our definition of “movable” and that of the owners were different.
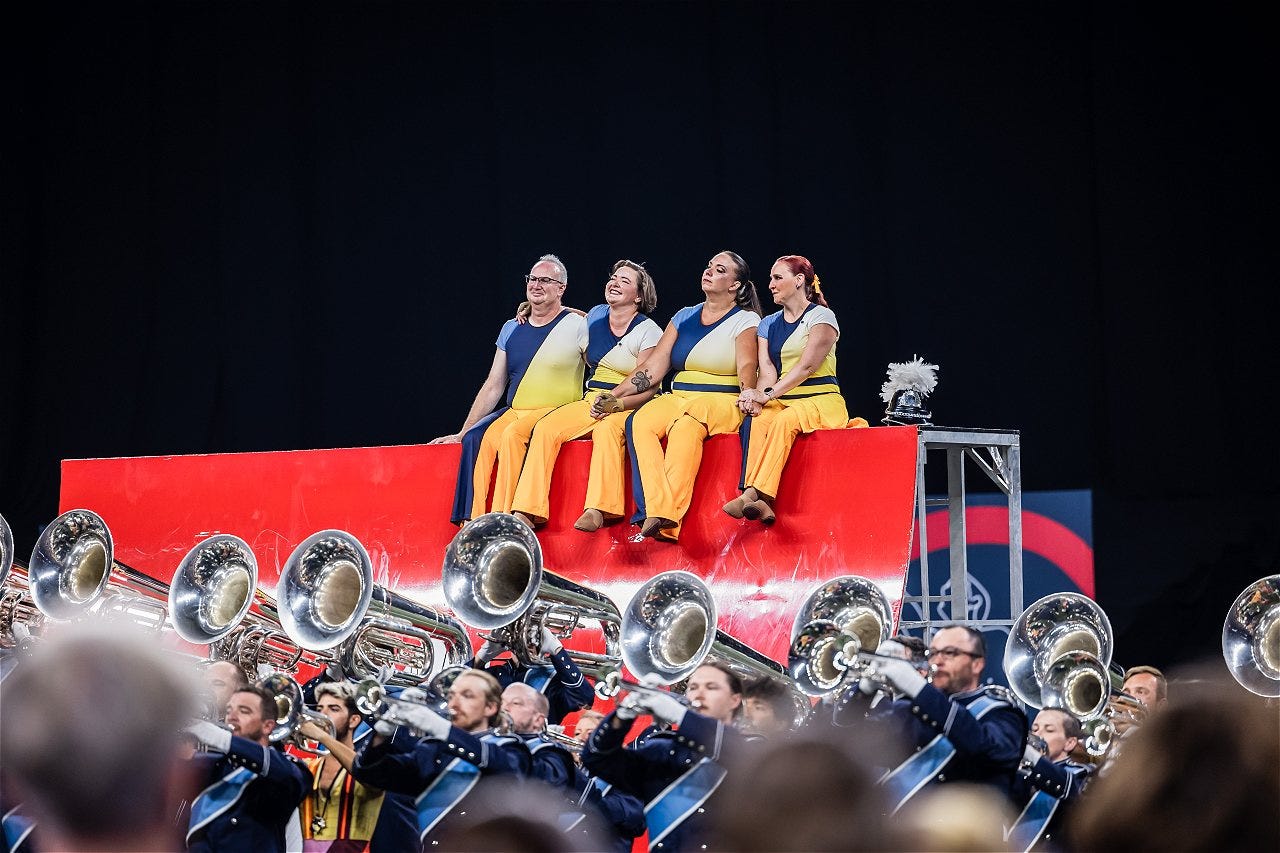
We also saw that about 2 feet of aluminum bracing was added to the prop in the modification (that we overlooked in the e-mail). This made it so that a performer could safely stand on the top of the ramp (the original mobile slides only had about 18 inches of space to stand). But it also changed the dimensions of the slide. But the immediate concern was that the slides could not be used as intended in the show. Right away Allen Marshall began to brainstorm how we could fix this and what it would take.
At the same time, we eyeballed the “prop trailer” and started wondering if it was going to fit in that trailer. Mike Bonnell pulled out measuring tape and found that we had another problem. The trailer we took the ramp off had doors that swung out, the trailer it was going on had a roll-top. Would it fit? We found that pushing the rolltop all the way up would give us enough clearance. So we thought we were good.
In the meantime, Team Unload started peeling the former band’s vinyl off the slides. One of the other modifications they made was hand holds on the slide facing. This would later become an issue for applying the vinyl. We left the Bingo Hall on Sunday, five days before move-in, with some ideas for fixing the mobility issue.
On Monday after talking with Larry Hershman, I called our resident team engineer, Ted Swaldo, about the problem. He met me at the Bingo Hall at the end of the work day and we talked through what we needed to do to move the wheels. It would take a person with a portable welder to come out and attach plates to the bottom of the ramp and then transfer the four wheels over to the new plates. This endeavor would end up requiring an electrician to do a temporary high voltage wiring job to the Bingo Hall and then for the welder to put the plates on. David Glasgow facilitated this happening at the Bingo Hall.
Ted made this all happen in a day and he picked up the cost personally.
On Wednesday, Allen Marshall and Anthony 'Duck' Mallard swapped the tires from the back to the bottom. Then our next dilemma. By moving the wheels to the bottom, when the final part of the slide was dropped into place, it would hang 12 inches off the ground and make it unstable for sliding down. We would need to figure out a way to block the slide bottom if we were to use it. Allen Marshall was on it.
But it was on Wednesday we discovered the next big problem, which was the ramps were not going to fit on the “prop trailer” we had in the lot. While there was clearance for the rolltop above, we never checked the lateral clearance. Because of the rolltop railing, the steel frame on the back of this trailer was narrower than the trailer the props came on. We needed 96” of width. The rolltop trailer had 94”. The slides weren’t going on that trailer.
Our two trailers came courtesy of Young’s Trucking in Canton. They have long been a partner with Bluecoats stretching back into the early 1990s. Zach Young, the son of the original owner, marched Bluecoats in the early 2000s and now is the company owner. He was also marching in the Alumni Corps. I reached out to him right away with our problem. Again, we called David Glasgow to march the two blocks from his house to problem solve this with us. On speaker phone with Zach, we came to two options: find a trailer with a swing gate (like they came in on) or lashing them to a flatbed trailer.
The corps would be moving into the dorms in less than 48 hours and the first rehearsal would be in 72.
While it seems simple, the flatbed trailer would have had complications. The architecture of the props would mean that they would provide problems at high speed on the interstate and could be dangerous. They would need to be set on the flatbed sideways for the wind to freely move between the support aluminum framing. The slides facing forward or back could actually contribute to flipping the trailer over once on the highway. But Young’s had no swing gate trailers on their property and none they could easily access. Throughout Thursday we thought a flatbed would be the resolution. Loading it on and off would make it a big crew task because the width of the slides sideways exactly met the width of the flatbed trailer. Rolling it up and on and spinning it might not work. It would have to be muscled up each time. We’d also have to lash the 16 backdrop frames and 16 backdrop frame bases onto the flatbed. It would be extra time to do so.
On Friday, the day of move-ins, Zach Young was able to do the near-impossible and working the phones like crazy was able to locate a swing gate trailer we could use in the eastern Cleveland suburbs. But we would have to go get it by 5 pm on Friday. Kevin Stone arrived for check-in just in the nick of time to register, drop his stuff in the dorm and go fetch this trailer 45 minutes away before 5 pm and bring it back to Akron.
But the slides were still at the Bingo Hall in North Canton.
Prior to rehearsal starting on Saturday morning, we recruited some “young blood” to help load the props ASAP at the Bingo Hall. While waiting for the help, Allen Marshall went to work installing four legs on each slide extension so they could be used with stability. He had fabricated and welded the legs and screwed them into the extension. Overnight. The ramps were now usable if we could get them to rehearsal.
This load crew was mostly vets who marched in ‘18, ‘19, and ‘21. When they saw the slides at the Bingo Hall they immediately became fanboys and girls and had to try out the slides while awaiting the new trailer. The very definition of giddy. When the trailer arrived it was a quick and simple process to load them and off they went to rehearsal. Later that day they were moved to the field to incorporate into the show.
At which point the NEXT problem arose. Only two of the four wheels swiveled.
This makes it easy for a few people to move the prop into a position, but the location of the swivel wheels made it difficult to open the two slides to “reveal” the drum line behind it. It worked, but it wasn’t easy or the way intended. Moving the slides across the field together and then swiveling them later for the show was also going to be a problem. Resolving this as the wheels were would require drill changes.
Of course, the idea of swapping wheels with the backdrop frames would be the easiest solution. Nope. Different sized wheel architecture. So we would need to go find the right size wheels. This is not a Home Depot job. We hoped maybe they would be at a truck stop. But Kevin Stahl got on the phone Sunday, day 2 of rehearsals, and was able to reach a contact in New Philadelphia who had the right wheels to match the swivel wheels we had. Not only were they currently working on a prop in the area, they had the right tires and could drop them off in Akron that afternoon.
By Sunday night the props now were movable with the right wheels and functional as slides. Now came the fine-tuning. Ben Gunnarson had a hook installed on the slide in 2016 so he could quickly swap out his trumpet for the Fluegel. Again, Allen Marshall was on it. And because of the previous modifications made to the top of the slide, where people stood, Ben couldn’t quickly grab anything to get into position to play on time. We needed to cut handholds in the top for him. Allen Marshall to the rescue once again. We also needed to put a bin of some sort within the aluminum framework so the guard could drop their flags on it and not have them fall out when moving the slide. Allen had this figured too.
By Monday lunch, the slides would just need the vinyl applied (and show step-off was now 10 hours away). The vinyl also arrived at the last second the day before move-ins.
But applying the vinyl needed to be left to the experts and John Millsap is Bluecoats expert. The vinyl didn’t start to go on until Monday (show day!) mid-day. The problem Millsap faced was the holes cut into the slide to assist in climbing it by the band we got these from. Covering the holes with vinyl would lead to shredding the vinyl when slid down. Cutting the vinyl around the holes might lead to a “cheese grater” effect on the person sliding (or having to perfectly aim their slide). So Millsap taped each of the openings (slowing down the vinyl process) before applying the vinyl.
At more than one point in the process, it was felt we were going to have to abandon the ramps. From even making it to Canton on time to then what had to happen to get them usable and movable. It’s a testament to the will of this organization when faced with a challenge to explore all the possibilities and exhaust all resources. Nobody simply gave up. Would the show have been as special as it was without the ramps? Probably. But it’s that commitment to excellence and adding those little touches that separate great and amazing. Without Ted, Kevin, Millsap, and especially Allen, those beautiful ramps that meant so much to the program would have been scrap aluminum sitting in the Bingo Hall parking lot.
The 2022 Bluecoats Alumni Corps marked the 50th anniversary of the Bluecoats Drum and Bugle Corps. The Alumni Corps featured 425 former marching members of the Bluecoats and the Glassmen Drum and Bugle Corps performing Bluecoats classics spanning the decades.
What a great story! And that alumni show was EVERYTHING!